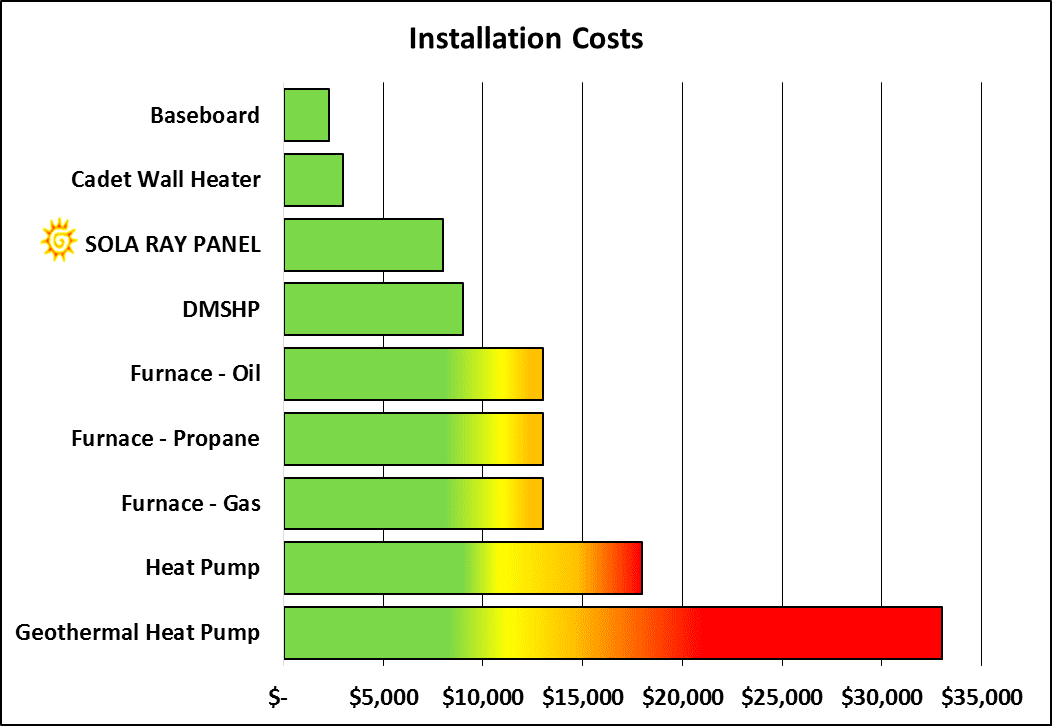
In today's rapidly evolving technological landscape, businesses often face significant financial decisions regarding equipment purchases and installations. One critical aspect of these decisions is understanding installation costs, which can dramatically impact the overall budget. This article delves into the installation costs of equipment that would total $217,000 over five years, providing insights into what influences these costs and how businesses can manage them effectively.
The importance of budgeting for installation costs cannot be overstated. With the right knowledge, businesses can avoid unexpected expenses and ensure that their investments yield the highest return. This article will explore various factors that contribute to installation costs, the implications of these expenses, and strategies for effective planning.
As we navigate through this comprehensive analysis, we will also look at the long-term benefits of understanding installation costs, providing readers with actionable insights to enhance their financial planning processes. Whether you're a small business owner or part of a large corporation, the information presented here will be valuable in making informed decisions about equipment investments.
Table of Contents
Understanding Installation Costs
Installation costs refer to the expenses associated with setting up new equipment within a business. These costs can vary widely depending on several factors, including the type of equipment, the complexity of the installation, and the location of the installation site. Understanding these costs is essential for effective financial planning.
Components of Installation Costs
- Labor Costs: Wages for technicians and engineers who perform the installation.
- Equipment Costs: The purchase price of the equipment being installed.
- Material Costs: Any additional materials required for the installation process.
- Overhead Costs: Indirect costs associated with the installation, such as utilities and administrative expenses.
Factors Influencing Installation Costs
Several factors can significantly influence the total installation costs of equipment. Understanding these factors can help businesses better prepare their budgets and avoid unexpected expenses.
Type of Equipment
The type of equipment being installed plays a crucial role in determining installation costs. For example, heavy machinery may require specialized installation techniques and more skilled labor, leading to higher costs.
Installation Complexity
Complex installations, such as those involving multiple components or advanced technology, can increase labor costs and time, ultimately driving up overall expenses.
Location of Installation
The geographical location of the installation can also impact costs. Remote locations or areas with high living costs may require more significant investment in labor and logistics.
Long-Term Costs and Benefits
When considering installation costs, it’s essential to look beyond the immediate expenses and assess the long-term implications. While the initial installation of equipment may seem high, it’s crucial to evaluate the potential return on investment (ROI) over time.
Projected Maintenance Costs
Over the lifespan of the equipment, maintenance costs will also contribute to the overall expense. Regular maintenance can help mitigate larger repair costs in the future and extend the equipment's lifespan.
Operational Efficiency
Investing in quality equipment with higher installation costs may lead to improved operational efficiency, which can result in cost savings in other areas of the business.
Budgeting for Installation Costs
Effective budgeting for installation costs is vital for any business planning to invest in new equipment. Here are some strategies to consider:
Conduct a Cost-Benefit Analysis
Businesses should perform a thorough cost-benefit analysis before proceeding with equipment purchases. This analysis should take into account both installation costs and potential savings from improved efficiency.
Set Aside Contingency Funds
It’s prudent to set aside contingency funds to cover any unexpected costs that may arise during the installation process.
Case Study Analysis
To illustrate the impact of installation costs, let’s examine a hypothetical case study involving a manufacturing company that invested in new assembly line equipment.
Company Overview
- Name: XYZ Manufacturing Co.
- Industry: Manufacturing
- Location: Urban area with high labor costs
Installation Cost Breakdown
Over five years, XYZ Manufacturing Co. incurred $217,000 in installation costs. The breakdown is as follows:
- Labor Costs: $100,000
- Equipment Costs: $90,000
- Material Costs: $20,000
- Overhead Costs: $7,000
Strategies to Reduce Installation Costs
While installation costs can be significant, there are strategies businesses can employ to minimize these expenses.
Negotiate with Vendors
Businesses should consider negotiating with vendors for better pricing on installation services. Establishing long-term relationships with reliable vendors can also lead to discounts over time.
Train In-House Staff
Training in-house staff to handle installation and maintenance tasks can reduce reliance on external contractors, potentially lowering overall costs.
The Role of Vendors and Contractors
Vendors and contractors play a critical role in the installation process. Choosing the right partners can significantly impact installation costs and overall project success.
Selecting Reliable Contractors
Conducting thorough research and selecting contractors with a proven track record can help ensure a smooth installation process and avoid hidden costs.
Vendor Support and Warranty
Many equipment vendors offer installation support and warranties, which can provide additional peace of mind and reduce potential costs associated with equipment failure.
Conclusion
In conclusion, understanding the installation costs of equipment totaling $217,000 over five years is crucial for effective financial planning. By considering factors such as equipment type, installation complexity, and location, businesses can better anticipate expenses and make informed decisions.
We encourage readers to engage with this topic further by leaving comments, sharing their experiences, or exploring additional articles related to budgeting and equipment investments. Your insights are valuable to us!
Thank you for reading, and we look forward to welcoming you back to our site for more informative content!
ncG1vNJzZmivp6x7rLHLpbCmp5%2Bnsm%2BvzqZmm6efqMFuxc6uqWarlaR8qrrSrZilpJGptrC6jJymrKyjYrynecSqrKKonZq7tXnWqKylnF2pvLWty2Zpam9gZX2quoyfoK%2BdXa6yor7SZquhnV6dwa64