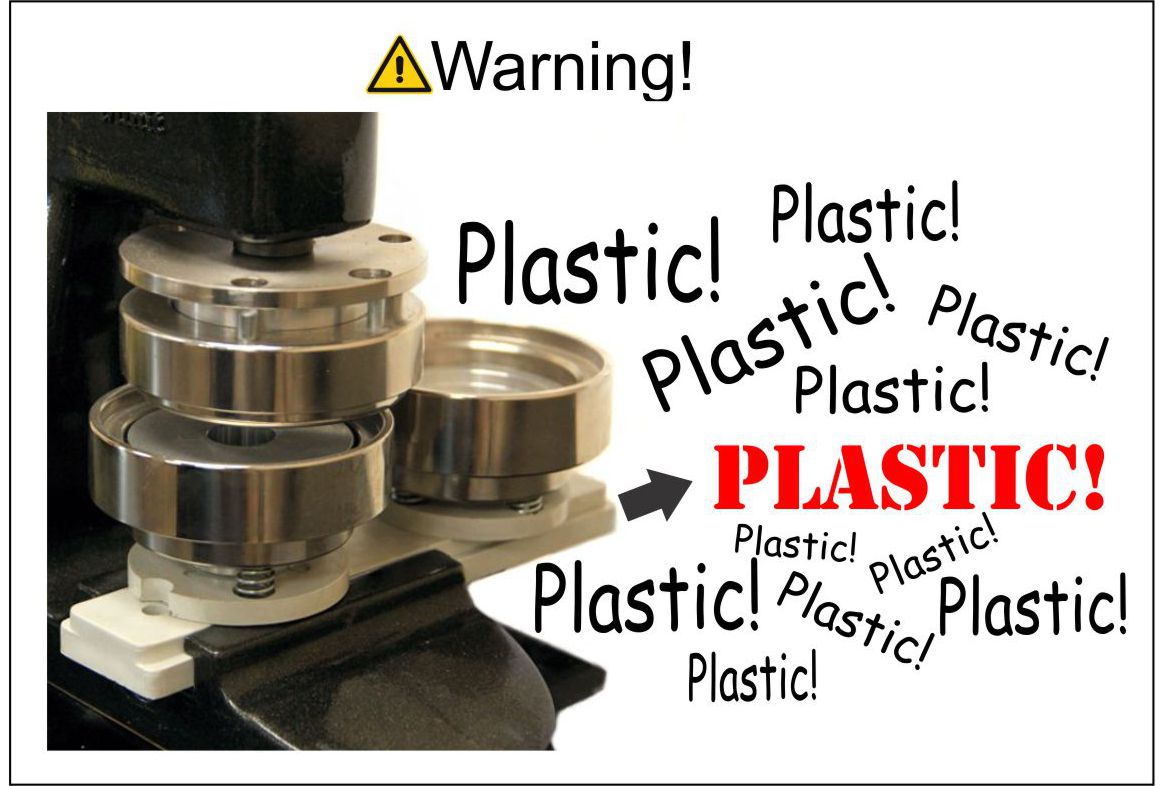
Plastic dies play a crucial role in modern manufacturing, particularly in the production of plastic components and products. As industries increasingly rely on plastic materials for various applications, understanding the intricacies of plastic dies becomes essential for engineers, manufacturers, and designers alike. In this article, we will explore the definition, types, applications, and benefits of plastic dies, alongside insights into their manufacturing processes and market trends.
The use of plastic dies is not just limited to one sector; they are integral to automotive, consumer goods, electronics, and medical fields. As the demand for high-quality and precise plastic parts continues to grow, the significance of plastic dies in ensuring efficiency and accuracy in production cannot be overstated. This article will delve into the various aspects of plastic dies, providing a detailed overview aimed at both industry professionals and enthusiasts alike.
Throughout this guide, we will also address common questions and misconceptions surrounding plastic dies, supported by data and statistics from reputable sources. By the end of this article, readers will have a comprehensive understanding of plastic dies, enabling informed decisions in their respective fields.
Table of Contents
1. What are Plastic Dies?
Plastic dies are specialized tools used in the manufacturing process to shape and form plastic materials into desired products. These dies are crucial in processes such as injection molding, extrusion, and blow molding. Their primary purpose is to ensure that the plastic is shaped accurately and consistently, allowing manufacturers to produce high-quality parts efficiently.
In essence, plastic dies function similarly to metal dies used in metalworking. However, they are designed specifically to handle the unique properties of plastic, such as its viscosity and thermal behavior. This makes the design and manufacturing of plastic dies a specialized field that requires expertise in both material science and engineering.
2. Types of Plastic Dies
There are several types of plastic dies, each tailored for specific manufacturing processes. The choice of die largely depends on the end product's requirements, including size, shape, and production volume. Below, we discuss the most common types of plastic dies.
2.1 Injection Molding Dies
Injection molding dies are among the most widely used types of plastic dies. They are designed to inject molten plastic into a mold cavity, where it cools and solidifies into the desired shape. This process is highly efficient for producing large quantities of identical parts.
- Key Features:
- High precision and repeatability.
- Can accommodate complex geometries.
- Suitable for a wide range of plastic materials.
2.2 Extrusion Dies
Extrusion dies are used in the extrusion process, where plastic is melted and forced through a die to create continuous shapes, such as sheets, films, or tubes. The design of extrusion dies is crucial for maintaining uniform thickness and consistency in the final product.
- Key Features:
- Ideal for producing long, continuous products.
- Variety of shapes and profiles possible.
- Efficient for high-volume production.
2.3 Blow Molding Dies
Blow molding dies are used to create hollow plastic parts, such as bottles and containers. In this process, air is blown into a heated plastic tube, expanding it against the walls of a mold. This technique is particularly effective for producing lightweight and durable packaging solutions.
- Key Features:
- Excellent for producing hollow shapes.
- Cost-effective for large-scale production.
- Allows for customization in design.
2.4 Compression Molding Dies
Compression molding dies are utilized in a process where plastic is heated and then compressed into a mold. This method is often used for thermosetting plastics and is known for producing strong and durable parts.
- Key Features:
- Effective for high-strength applications.
- Good for producing large, simple shapes.
- Less waste compared to other methods.
3. Applications of Plastic Dies
Plastic dies are used across various industries, showcasing their versatility and importance in modern manufacturing. Here are some of the primary applications:
- Automotive Parts: Used to manufacture components like dashboards, bumpers, and interior trim.
- Consumer Goods: Found in toys, appliances, and packaging materials.
- Electronics: Essential for producing casings and components for devices.
- Medical Devices: Used in the creation of syringes, containers, and other critical medical components.
4. Manufacturing Processes of Plastic Dies
The manufacturing process of plastic dies involves several key steps to ensure precision and durability. Here are the main stages:
- Design: Engineers create detailed CAD models of the die.
- Material Selection: Choosing suitable materials to withstand the molding process.
- Machining: Using CNC machines to shape the die according to specifications.
- Assembly: Components are assembled and tested for fit and function.
Manufacturers often employ advanced technologies such as 3D printing and simulation software to enhance the design process and reduce lead times.
5. Benefits of Using Plastic Dies
Utilizing plastic dies offers numerous advantages that contribute to efficient manufacturing processes:
- Cost-Effectiveness: High-volume production reduces per-unit costs.
- Versatility: Capability to produce a wide range of shapes and sizes.
- Precision: Ensures high accuracy and repeatability in production.
- Reduced Waste: Optimizes material usage, minimizing waste during production.
6. Current Market Trends
The plastic die market is continuously evolving, influenced by advancements in technology and shifting consumer demands. Some current trends include:
- Increased Adoption of Automation: Streamlining production processes.
- Sustainability Efforts: Growing focus on eco-friendly materials and practices.
- Customization: Rising demand for tailored solutions to meet unique requirements.
7. The Future of Plastic Dies
As industries move towards more sustainable practices, the future of plastic dies will likely involve innovations that prioritize energy efficiency and reduced environmental impact. Technologies such as bioplastics and advanced manufacturing methods will shape the next generation of plastic dies.
8. Conclusion
In summary, plastic dies are integral to the manufacturing of plastic products, playing a vital role in various industries. Understanding the different types of plastic dies and their applications can significantly impact production efficiency and quality. As the market continues to evolve, staying informed about trends and innovations in plastic dies is essential for manufacturers and engineers alike.
If you found this article insightful, feel free to leave a comment or share it with colleagues. For more information on related topics, explore our other articles on manufacturing technologies.
Thank you for reading, and we look forward to welcoming you back for more informative content!
ncG1vNJzZmivp6x7rLHLpbCmp5%2Bnsm%2BvzqZmrJmUl7yzfY6po5qrpJ6wbrDInqpnoKSiuQ%3D%3D