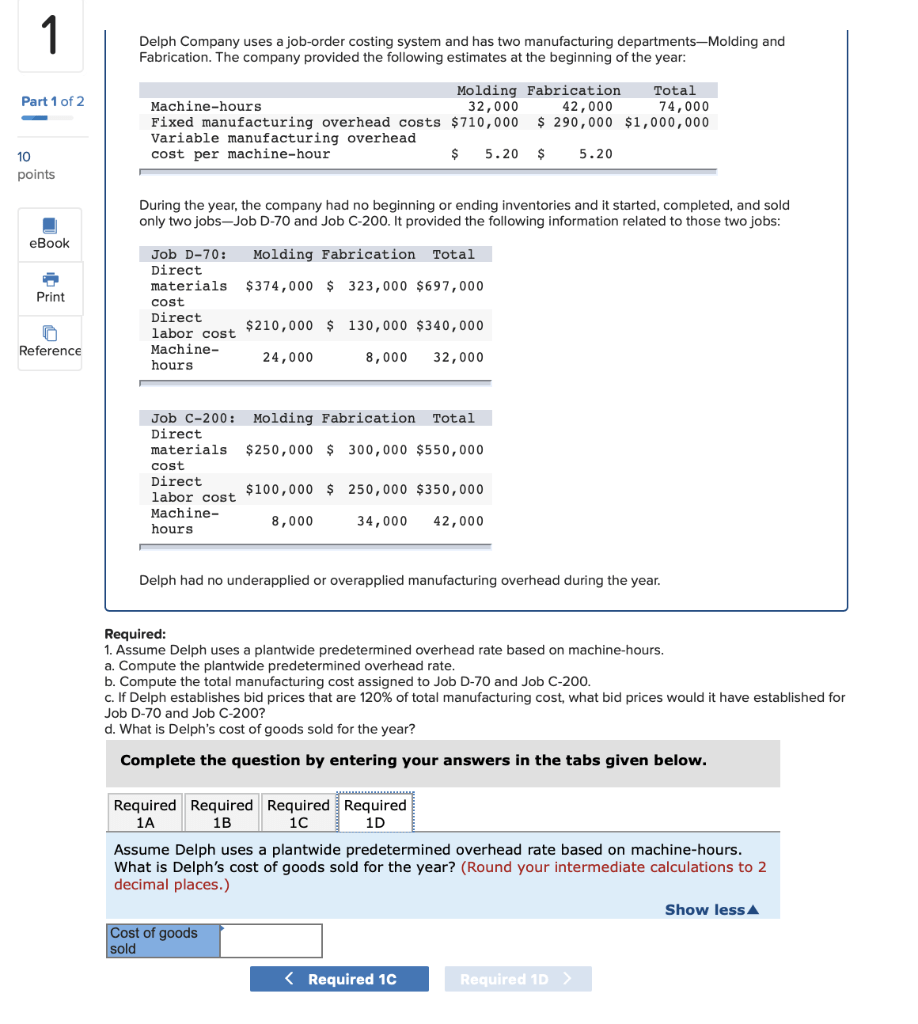
Delph Company utilizes a job-order costing system, a method that plays a crucial role in accurately tracking production costs for its various manufacturing projects. This cost accounting system is particularly beneficial for businesses that produce distinct, customized products, allowing them to determine the exact cost associated with each specific job. By understanding job-order costing, companies like Delph can manage resources effectively, control expenses, and enhance overall profitability.
In this article, we will delve deep into the intricacies of job-order costing as implemented by Delph Company, highlighting its significance, components, and the benefits it brings to the manufacturing process. We will also explore how the job-order costing system aids in financial decision-making and strategic planning for the company.
Furthermore, we will provide a detailed examination of Delph Company's manufacturing operations, showcasing how the job-order costing system is integrated into their workflow. Whether you are a business owner, financial analyst, or student of accounting, this comprehensive overview will equip you with the knowledge necessary to understand the importance of job-order costing in today’s competitive market.
Table of Contents
What is Job-Order Costing?
Job-order costing is an accounting system used to assign manufacturing costs to specific production jobs. This method is essential for companies like Delph that produce unique products tailored to individual customer specifications. In contrast to process costing, which averages costs over continuous production, job-order costing allows for precise tracking of costs associated with each distinct job.
The job-order costing system involves accumulating costs for direct materials, direct labor, and manufacturing overhead incurred during the production of each job. This helps Delph Company to determine the total cost of production for each unique order, allowing for accurate pricing and profitability analysis.
Importance of Job-Order Costing
The significance of job-order costing cannot be understated, especially for companies engaged in customized manufacturing. Some key points include:
- **Precision in Costing**: Job-order costing provides a clear picture of the costs associated with each job, enabling better financial control.
- **Enhanced Decision-Making**: With accurate cost data, management can make informed decisions regarding pricing, budgeting, and resource allocation.
- **Performance Evaluation**: Job-order costing allows for the evaluation of job profitability and efficiency, helping in identifying areas for improvement.
How Delph Company Uses Job-Order Costing
Delph Company employs a job-order costing system to manage its two distinct manufacturing operations efficiently. These operations can be categorized based on the nature of the products being produced:
1. Custom Manufacturing
In custom manufacturing, Delph creates products based on specific customer requests. Each job is unique, and costs are tracked meticulously using job-order costing to ensure accurate pricing and profitability.
2. Batch Manufacturing
For batch manufacturing, Delph produces a limited quantity of products simultaneously. Despite the similarity in products, each batch may incur different costs, making job-order costing vital for tracking expenses accurately.
Components of Job-Order Costing
The job-order costing system consists of several key components:
- Direct Materials: The raw materials specifically used for each job.
- Direct Labor: The labor costs directly associated with the production of each job.
- Manufacturing Overhead: Indirect costs related to production that cannot be traced directly to a specific job, such as utilities and depreciation.
Benefits of Job-Order Costing
Implementing a job-order costing system offers numerous advantages for Delph Company:
- **Improved Cost Control**: By accurately tracking costs for each job, Delph can identify and eliminate wasteful practices.
- **Custom Pricing Strategies**: With detailed cost information, Delph can develop competitive pricing strategies tailored to each customer’s needs.
- **Increased Customer Satisfaction**: The ability to provide precise quotes and track job progress enhances customer trust and satisfaction.
Job-Order Costing Implementation in Manufacturing
The implementation of job-order costing within Delph Company’s manufacturing processes involves several steps:
- **Job Identification**: Each job is assigned a unique job number for tracking.
- **Cost Accumulation**: Costs are gathered throughout the production process, including materials, labor, and overhead.
- **Job Cost Sheet**: A job cost sheet is maintained for each job, summarizing all incurred costs.
- **Cost Analysis**: After job completion, a thorough analysis is conducted to compare estimated costs against actual costs.
Challenges of Job-Order Costing
While job-order costing is beneficial, it also presents certain challenges:
- **Complexity in Cost Allocation**: Allocating overhead costs can be complicated, leading to potential inaccuracies.
- **Time-Consuming Process**: Tracking costs for each job can be labor-intensive and requires diligent record-keeping.
- **Variability in Costs**: Fluctuations in material prices and labor rates can complicate cost estimation.
Conclusion
In conclusion, Delph Company’s use of a job-order costing system is integral to its manufacturing operations, enabling accurate cost tracking and enhanced decision-making. By understanding the components, benefits, and challenges of job-order costing, businesses can leverage this system to improve financial performance and customer satisfaction. We encourage you to leave your thoughts in the comments below, share this article, or explore more on our site to deepen your understanding of cost accounting practices.
Thank you for reading! We hope to see you back here for more insightful articles.
ncG1vNJzZmivp6x7rLHLpbCmp5%2Bnsm%2BvzqZmm6efqMFuxc6uqWarlaR8pbHLqZ9mm5%2BivaK62GasrJ2jYq5uts6bZKiqlJq%2Fbq%2FOrKuippdiwLq%2F056kZpmemXqprdJmq7CnXaKur8HFmpqtraKeu6h6x62kpQ%3D%3D