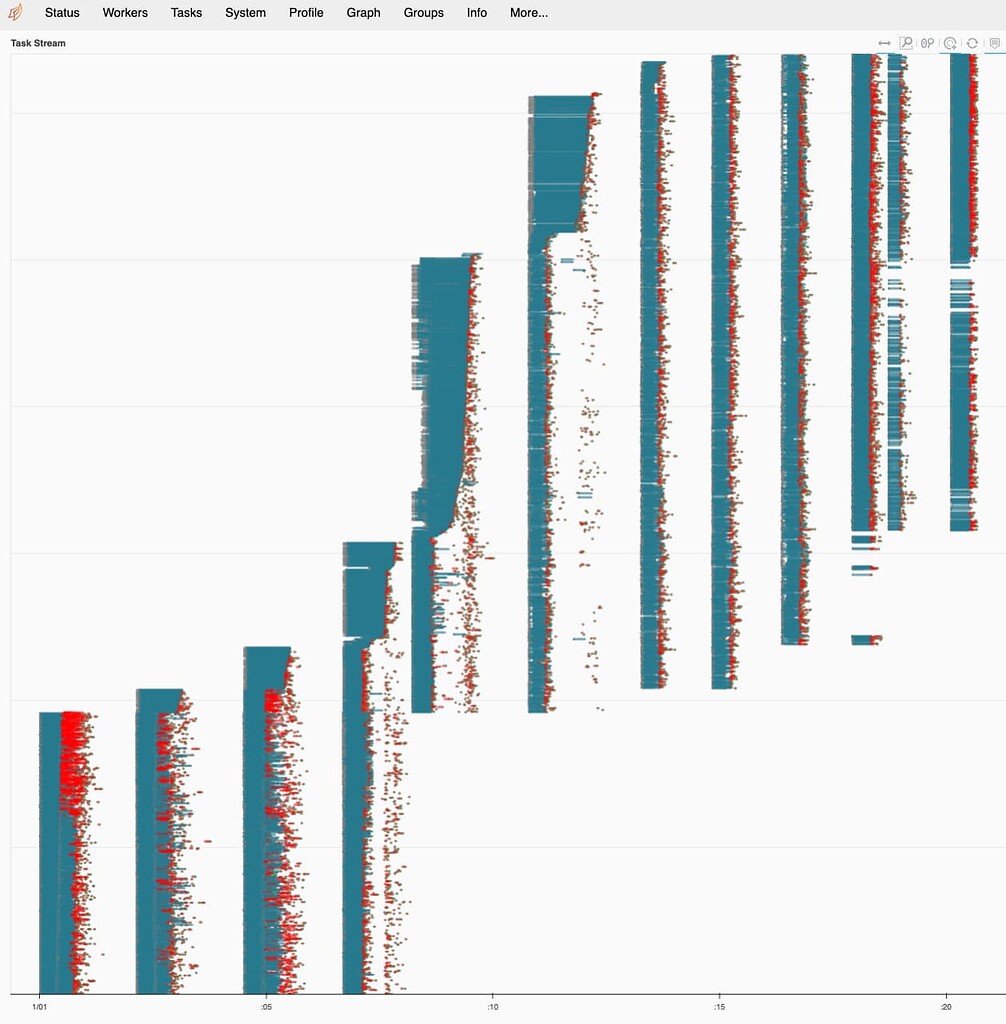
Idle time is an essential concept in the world of business and operations management. It refers to the periods when resources, such as labor or machinery, are not utilized effectively in the production process. Understanding idle time is crucial for organizations as it can lead to increased costs and reduced efficiency. In this article, we will explore the significance of idle time, its implications on support and process approaches, and strategies to minimize it.
As businesses strive to improve operational efficiency, identifying and addressing idle time becomes a priority. This article delves into the various aspects of idle time, including its definition, causes, and the impact it has on overall productivity. By understanding idle time and its relation to support and process approaches, organizations can implement effective strategies to enhance performance.
Moreover, we will provide a comprehensive overview of how support systems and process approaches can be utilized to mitigate the effects of idle time. With a focus on practical solutions and real-world examples, this article aims to equip business leaders and managers with the knowledge necessary to optimize their operations.
Table of Contents
Definition of Idle Time
Idle time can be defined as the time during which labor or machinery is not in productive use. This can occur for various reasons, including equipment breakdowns, lack of materials, or inefficient scheduling. In essence, idle time represents wasted resources that do not contribute to the output of goods or services.
Types of Idle Time
- Voluntary Idle Time: This occurs when workers are temporarily not engaged in productive work due to their own choice, such as breaks or waiting for instructions.
- Involuntary Idle Time: This happens due to external factors beyond the control of workers, such as equipment failures or supply chain disruptions.
Causes of Idle Time
Understanding the causes of idle time is essential for businesses looking to reduce it. Some common causes include:
- Equipment Failures: Breakdowns or maintenance can halt production processes.
- Supply Chain Issues: Delays in receiving materials can lead to idle time.
- Poor Scheduling: Inefficient scheduling can result in workers being underutilized.
- Training and Skill Gaps: Lack of training can lead to inefficiencies in the production process.
Impact of Idle Time on Business
Idle time can have significant repercussions for businesses, including:
- Increased Costs: Wasted labor and machinery time directly affect the bottom line.
- Decreased Productivity: When resources are not utilized effectively, overall productivity suffers.
- Lower Employee Morale: Employees may feel demotivated when they are not actively contributing to the production process.
Support Systems in Managing Idle Time
Support systems play a crucial role in managing idle time. These systems can include:
- Maintenance Management Systems: Regular maintenance schedules can help prevent equipment failures.
- Inventory Management Systems: Efficient inventory systems ensure that materials are available when needed.
- Training Programs: Providing training can fill skill gaps and reduce inefficiencies.
Process Approach to Reduce Idle Time
The process approach focuses on optimizing workflows to minimize idle time. This can involve:
- Streamlining Processes: Analyzing and improving workflows can reduce delays.
- Implementing Lean Principles: Lean methodologies aim to eliminate waste, including idle time.
- Utilizing Technology: Automation and technology can enhance efficiency and reduce idle time.
Strategies to Minimize Idle Time
Organizations can implement various strategies to minimize idle time, such as:
- Conducting Regular Audits: Assessing processes regularly can identify areas of improvement.
- Encouraging Employee Feedback: Employees can provide valuable insights into inefficiencies.
- Investing in Technology: Tools like ERP systems can improve coordination and reduce idle time.
Case Studies on Idle Time Reduction
Several organizations have successfully reduced idle time through targeted strategies. For instance:
- Case Study 1: A manufacturing company implemented a predictive maintenance program, reducing equipment-related idle time by 30%.
- Case Study 2: A logistics firm optimized its supply chain processes, leading to a 25% decrease in idle time across operations.
Conclusion
In summary, idle time is a critical factor that can impact a business's efficiency and profitability. By understanding its causes and effects, organizations can implement effective support and process approaches to minimize idle time. It is essential for business leaders to be proactive in identifying idle time and taking steps to mitigate it. We invite you to leave your thoughts in the comments, share this article, or explore more content on our site.
Thank you for reading! We hope you found this article informative and beneficial. Please feel free to return for more insights and guidance on optimizing your business operations.
ncG1vNJzZmivp6x7rLHLpbCmp5%2Bnsm%2BvzqZmm6efqMFuxc6uqWarlaR8qrDLnmStoZ2aeqR50q6nqaeiqXqlec%2Brppydo6h6orzPq6aam5hjtbW5yw%3D%3D