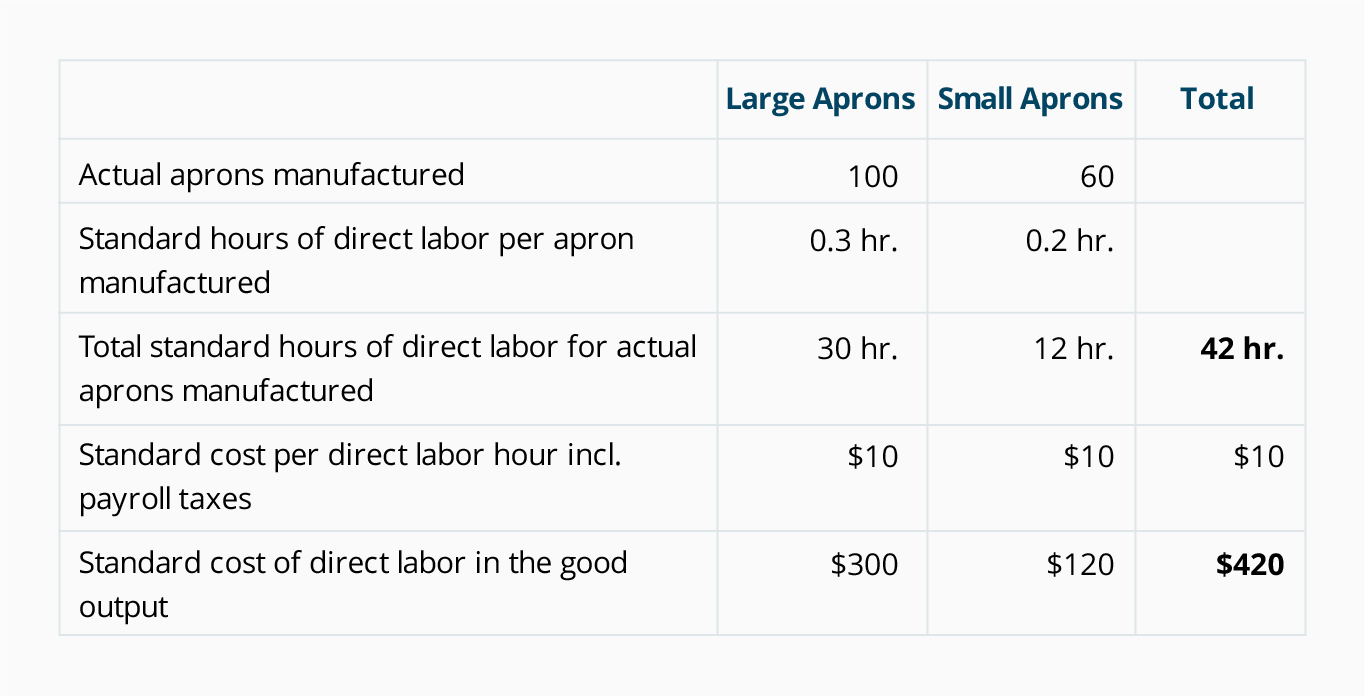
Total annual direct labor hours are a critical metric in assessing workforce productivity and efficiency. Companies rely on accurate labor hour calculations to manage costs, optimize workflows, and enhance overall performance. The figure of 96,300 hours is significant, especially when dissecting its components, like the calculation of 1.5 hours per employee based on a workforce of 54,000 to 10,200. This article will explore the implications of this statistic, its calculation, and how organizations can leverage this data for better operational strategies.
In today's competitive business landscape, understanding labor hours is not just about numbers; it’s about making informed decisions that can lead to growth and sustainability. By examining the total annual direct labor hours, companies can identify trends, allocate resources more effectively, and ultimately improve profitability. This article will provide a detailed breakdown of the 96,300 labor hours figure, its significance, and how it impacts various industries.
As we delve deeper into this topic, we will cover various aspects, including methods of calculation, factors influencing labor hours, and strategies for optimizing workforce efficiency. With the right insights, organizations can not only understand their labor metrics but also implement changes that foster a productive work environment.
Table of Contents
What are Direct Labor Hours?
Direct labor hours refer to the total time employees spend directly engaged in the production of goods or services. This metric is essential for businesses to evaluate productivity and efficiency. Understanding direct labor hours helps organizations to:
- Calculate labor costs accurately.
- Identify areas for improvement in production processes.
- Assess employee performance and productivity.
Importance of Labor Hour Tracking
Tracking labor hours is crucial for several reasons:
- Cost Management: Accurate tracking of labor hours helps in managing payroll and controlling costs.
- Resource Allocation: Understanding labor hour distribution allows for effective workforce planning.
- Performance Evaluation: It enables businesses to evaluate employee performance and identify training needs.
Calculating Total Labor Hours
The calculation of total labor hours can be complex, involving various factors such as the number of employees, their working hours, and specific labor agreements. For instance, if we consider the example of 1.5 hours per employee based on a workforce of 54,000 to 10,200, the calculations can be represented as follows:
Formula for Calculation
The formula to calculate total annual direct labor hours is:
Total Labor Hours = Number of Employees × Average Working Hours per Employee
Example Calculation
For a workforce of 54,000 employees working an average of 1.5 hours per day over a year, the calculation would be:
- 54,000 employees × 1.5 hours/day × 365 days = 29,565,000 hours annually.
Conversely, with a workforce of 10,200, the calculation would yield:
- 10,200 employees × 1.5 hours/day × 365 days = 5,583,000 hours annually.
Factors Affecting Labor Hours
Several factors can influence the total annual direct labor hours:
- Seasonal Demand: Fluctuations in demand can lead to variations in labor hours.
- Employee Turnover: High turnover rates can disrupt productivity and affect total hours.
- Technological Advancements: Automation and technology can reduce the need for direct labor hours.
Strategies to Optimize Labor Hours
To enhance efficiency and reduce costs, organizations can implement several strategies:
- Training and Development: Investing in employee training can improve productivity.
- Process Improvement: Streamlining processes can help in reducing unnecessary labor hours.
- Utilizing Technology: Implementing tools for workforce management can enhance tracking and efficiency.
Case Study Analysis
Analyzing real-world examples can provide significant insights into the implications of total labor hours. For instance, a manufacturing company that implemented labor tracking software noted a 20% reduction in unnecessary overtime, leading to substantial cost savings. They achieved this by:
- Monitoring labor allocation in real-time
- Identifying underutilized resources
- Adjusting workforce schedules based on demand
Several tools are available for businesses to track labor hours efficiently:
- Time-tracking software (e.g., Toggl, Harvest)
- Project management tools (e.g., Trello, Asana)
- Workforce management systems (e.g., Deputy, Kronos)
Conclusion
Understanding total annual direct labor hours, particularly the significant figure of 96,300, is essential for organizations aiming to optimize their workforce. By accurately tracking labor hours, evaluating productivity, and implementing strategic improvements, businesses can enhance performance and profitability. We encourage readers to examine their own labor metrics and consider the strategies discussed in this article to drive positive change within their organizations.
We’d love to hear your thoughts! Please leave a comment below, share this article with your network, or check out other insightful articles on our site.
Thank you for reading, and we hope to see you back soon for more valuable insights!
ncG1vNJzZmivp6x7rLHLpbCmp5%2Bnsm%2BvzqZmm6efqMFuxc6uqWarlaR8tbvTmqNmmZ6jwqK4jJ2gq52TqXqtrcGoqWagn6q%2FtHnAq5xmcWZofXF5zqtkam1dnby2vtJmbG1oYGV6cnyRaWdnoKSiuQ%3D%3D