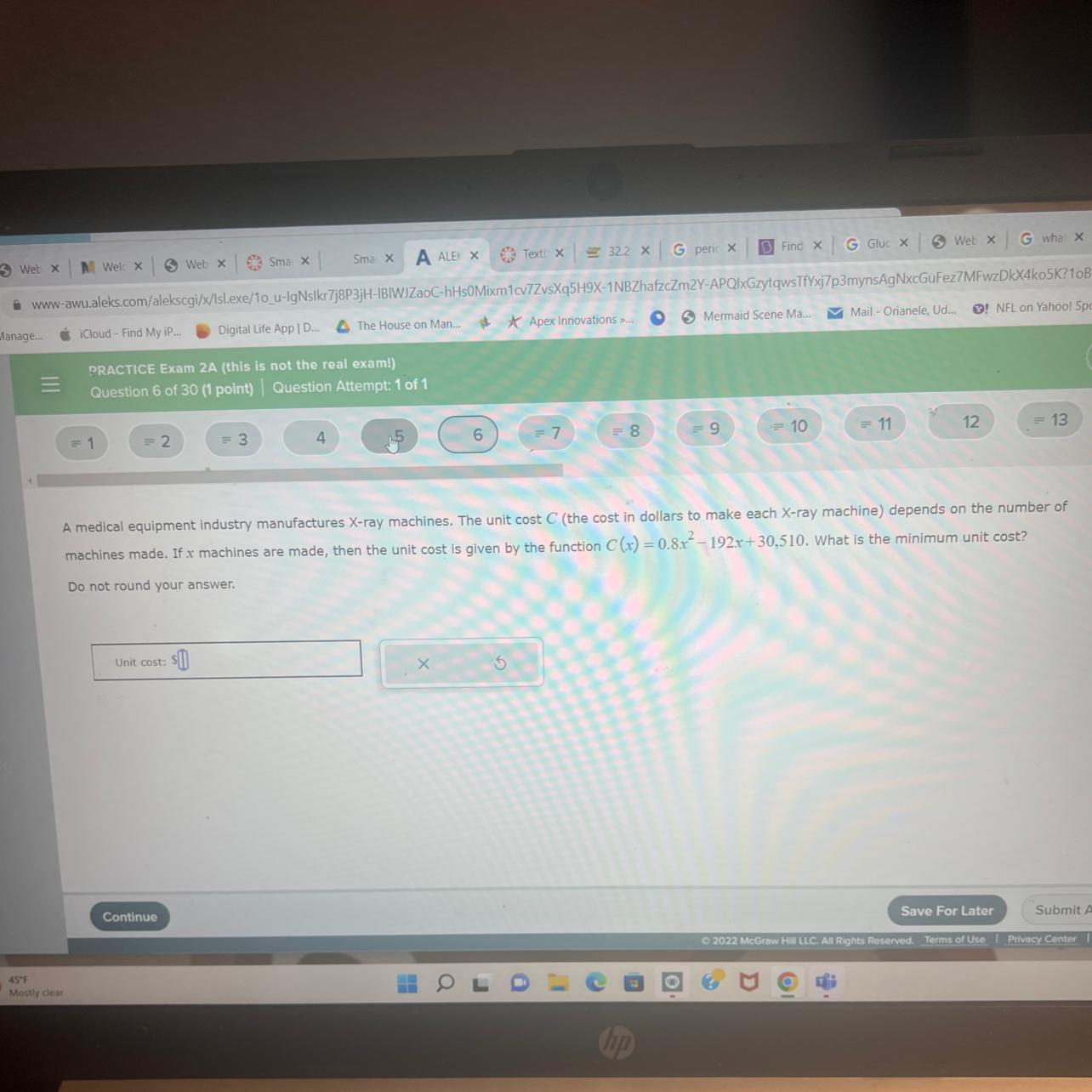
In the world of manufacturing, understanding the relationship between the number of machines produced and the unit cost is crucial for businesses looking to optimize their operations. This article will delve deep into how the production volume impacts unit costs, providing insights that are beneficial for manufacturers, entrepreneurs, and anyone involved in the production process. The concepts discussed here not only apply to manufacturing but also to various sectors where production cost is a critical factor.
With increasing competition and the need for efficiency, manufacturers often seek ways to reduce costs while maintaining quality. By exploring the relationship between the number of machines made and the unit cost, we can uncover strategies that lead to significant savings and improved profit margins. Understanding this dynamic can empower businesses to make informed decisions regarding production scale and resource allocation.
This comprehensive guide will cover critical aspects of production economics, including the principles of economies of scale, fixed versus variable costs, and the implications of production volume on overall profitability. Let’s embark on this journey to demystify how the number of machines made affects unit costs.
Table of Contents
Understanding Unit Cost
Unit cost refers to the total expenditure incurred by a company to produce, store, and sell one unit of a product. This cost is crucial for pricing strategies and profitability analysis.
To understand unit cost, consider the following components:
- Materials: The cost of raw materials used in production.
- Labor: Wages paid to workers involved in manufacturing.
- Overhead: Indirect costs such as utilities, rent, and administrative expenses.
By assessing these factors, businesses can determine their unit costs and strategize accordingly.
The Principle of Economies of Scale
Economies of scale refer to the cost advantages that businesses experience as they increase their production levels. The more units produced, the lower the cost per unit, leading to increased profitability.
Key aspects of economies of scale include:
- Operational efficiencies: Larger production volumes often lead to streamlined processes.
- Bulk purchasing: Buying materials in larger quantities often results in discounts.
- Specialization: Higher production levels can justify hiring specialized labor, improving productivity.
Fixed and Variable Costs Explained
Understanding fixed and variable costs is essential for calculating unit costs effectively. Here’s a breakdown:
Fixed Costs
Fixed costs remain constant regardless of the production volume. Examples include:
- Rent for manufacturing facilities
- Depreciation of machinery
- Salaries of permanent staff
Variable Costs
Variable costs fluctuate based on production levels. These include:
- Raw materials
- Hourly wages for temporary workers
- Utilities directly tied to production
The Impact of Production Volume on Unit Cost
The relationship between production volume and unit cost is direct. As production increases, the unit cost typically decreases due to the redistribution of fixed costs over a larger number of units. This phenomenon is crucial for manufacturers aiming to remain competitive.
Consider the following scenario:
- If a company produces 100 machines, the fixed costs of $10,000 will be distributed across 100 units, resulting in a fixed cost of $100 per machine.
- If the same company increases production to 1,000 machines, the fixed cost per unit drops to $10.
How to Calculate Unit Cost
Calculating unit cost involves a straightforward formula:
Unit Cost = (Total Fixed Costs + Total Variable Costs) / Number of Units Produced
Using this formula allows businesses to ascertain their unit costs accurately and make informed decisions regarding production levels and pricing strategies.
Case Studies: Real-World Applications
To illustrate the concepts discussed, let’s examine a few case studies of companies that successfully optimized their production processes:
Case Study 1: Automotive Manufacturer
An automotive manufacturer increased production from 10,000 to 100,000 units per year. As a result, the unit cost decreased by 25% due to economies of scale.
Case Study 2: Electronics Company
An electronics company streamlined its supply chain and reduced variable costs by 15%. This adjustment allowed for reduced unit costs even without increasing production volume.
Strategies for Reducing Unit Costs
Businesses can implement various strategies to reduce unit costs, including:
- Investing in technology to automate processes
- Negotiating better terms with suppliers
- Reviewing and optimizing the production process regularly
Conclusion
In conclusion, understanding the relationship between the number of machines made and the unit cost is essential for any manufacturing business. By applying the principles of economies of scale, recognizing fixed and variable costs, and utilizing effective cost-reduction strategies, companies can enhance their profitability and competitiveness in the market.
We encourage readers to share their thoughts on this topic, engage in discussions, and explore further articles on manufacturing and cost optimization.
Call to Action
If you found this article helpful, please leave a comment below, share it with your network, or explore our other resources for more insights into manufacturing and economics.
Thank you for reading, and we hope to see you back for more informative content!
ncG1vNJzZmivp6x7rLHLpbCmp5%2Bnsm%2BvzqZmm6efqMFuxc6uqWarlaR8tbTEZqWupZKav267xWakmpuYnrumv4ymmJ2dXZ6zbsSMppicoJmjsrR5wKucZqWRmbJuwMeepWasmJp6trrIrWScp6Opeqq%2FjaGrpqQ%3D