Flow gauge is an indispensable instrument in various industries, providing critical data on fluid movement. In today's fast-paced world, the accuracy and reliability of flow measurement are paramount for efficiency and safety. This article delves into the intricacies of flow gauges, their applications, benefits, and the technology behind them.
As industries evolve, the demand for precise flow measurement continues to grow. Understanding the principles and functionalities of flow gauges is essential for professionals in fields such as oil and gas, water management, and manufacturing. This article aims to equip you with comprehensive knowledge about flow gauges, ensuring you can make informed decisions about their implementation and maintenance.
Whether you are an engineer, technician, or a business owner, grasping the nuances of flow gauge technology will enhance your operational capabilities. Join us as we explore the fascinating world of flow gauges, their types, and their significance in various applications.
Table of Contents
What is a Flow Gauge?
A flow gauge is an instrument designed to measure the flow rate of liquids or gases within a system. It provides crucial data that helps in monitoring and controlling fluid dynamics. This information is vital for maintaining the efficiency of industrial processes and ensuring safety standards are met.
Key Components of a Flow Gauge
- Sensor: Detects the flow of fluid.
- Transmitter: Converts the detected flow into a readable signal.
- Display: Showcases the flow rate in various units such as liters per minute or gallons per hour.
Types of Flow Gauges
Flow gauges come in various types, each designed for specific applications and requirements. Understanding these types can help in selecting the appropriate gauge for your needs.
1. Mechanical Flow Gauges
Mechanical flow gauges operate using physical mechanisms, such as gears or floats, to measure flow. They are often used in simpler applications where precision is not the highest priority.
2. Electronic Flow Gauges
Electronic flow gauges utilize advanced technology to provide accurate measurements. They often feature digital displays and can be connected to other systems for better data integration.
3. Ultrasonic Flow Gauges
Ultrasonic flow gauges measure the flow of liquids and gases using sound waves. They are particularly useful for non-invasive measurement and can be highly accurate.
4. Magnetic Flow Gauges
Magnetic flow gauges, or magmeters, use electromagnetic principles to measure the flow of conductive fluids. They are widely used in water treatment and chemical processing.
How Flow Gauges Work
Understanding the operational principles of flow gauges is essential for effective usage. Each type of flow gauge operates on different principles, but the fundamental concept revolves around measuring the rate of fluid movement.
Principles of Operation
- Mechanical Gauges: Utilize physical movement to indicate flow rate.
- Electronic Gauges: Convert fluid flow into an electronic signal for processing.
- Ultrasonic Gauges: Measure the time it takes for sound waves to travel through the fluid.
- Magnetic Gauges: Measure flow based on the electromagnetic field created by the fluid's conductivity.
Applications of Flow Gauges
Flow gauges are utilized in numerous industries, each benefiting from accurate flow measurement. Here are some of the key applications:
1. Oil and Gas Industry
In the oil and gas sector, flow gauges help monitor and control the flow of crude oil, natural gas, and other fluids. Accurate measurement is critical for safety and efficiency in extraction and transportation.
2. Water Treatment Plants
Flow gauges are essential in water treatment facilities to ensure the proper flow of water through various stages of treatment. They help maintain water quality and compliance with environmental regulations.
3. Chemical Processing
In chemical manufacturing, flow gauges monitor the flow of raw materials and finished products. Precise measurement ensures product quality and process efficiency.
4. Food and Beverage Industry
Flow gauges are used in the food and beverage industry to measure the flow of ingredients, ensuring consistent quality and adherence to safety standards.
Benefits of Using Flow Gauges
Implementing flow gauges brings a multitude of benefits to various industries. Here are some of the key advantages:
- Improved Efficiency: Accurate flow measurement allows for optimized processes and resource management.
- Enhanced Safety: Monitoring flow rates helps identify potential issues before they escalate, ensuring operational safety.
- Regulatory Compliance: Many industries are required to maintain specific flow rates for compliance with environmental and safety regulations.
- Cost Savings: Efficient flow management reduces waste and operational costs, leading to significant savings in the long run.
Choosing the Right Flow Gauge
Selecting the appropriate flow gauge is crucial for achieving accurate measurements. Consider the following factors when choosing a flow gauge:
1. Type of Fluid
Different flow gauges are suited for specific types of fluids, such as viscous liquids, gases, or conductive fluids. Ensure that the gauge you choose is compatible with the fluid you are measuring.
2. Flow Rate Range
Consider the expected flow rate of your application. Different gauges have varying measurement ranges, so select one that fits your needs.
3. Installation Requirements
Evaluate the installation process and space constraints in your facility. Some flow gauges may require more sophisticated setups than others.
4. Budget Considerations
Determine your budget for purchasing and maintaining a flow gauge. Higher-end electronic gauges may offer more features, but traditional mechanical gauges can be more cost-effective for simpler applications.
Maintenance of Flow Gauges
Regular maintenance is key to ensuring the longevity and accuracy of flow gauges. Follow these best practices for optimal performance:
1. Regular Calibration
Calibrate flow gauges periodically to ensure accurate measurements. Calibration should be performed according to the manufacturer's guidelines.
2. Clean Sensors
Keep the sensors and components clean to prevent buildup that may affect readings. Regular cleaning schedules should be established based on usage and environmental conditions.
3. Inspect for Wear and Tear
Conduct routine inspections to identify any signs of wear or damage. Replace any worn components to maintain accurate performance.
4. Record Keeping
Maintain detailed records of maintenance activities, calibrations, and inspections. This documentation can be crucial for compliance and operational efficiency.
The Future of Flow Gauges
The future of flow gauges is promising, with advancements in technology paving the way for more efficient and accurate measurement solutions. Key trends to watch include:
1. Integration with IoT
The integration of flow gauges with Internet of Things (IoT) technology will allow for real-time monitoring and data analysis, enhancing decision-making processes.
2. Smart Sensors
Smart sensors equipped with AI capabilities will provide predictive analytics, helping to anticipate maintenance needs and improve overall efficiency.
3. Enhanced Data Analytics
As data analytics becomes more sophisticated, flow gauges will play an integral role in providing actionable insights for process optimization.
4. Eco-Friendly Solutions
The demand for sustainable solutions will drive innovations in flow gauge technology, focusing on energy efficiency and minimal environmental impact.
You Might Also Like
Elizabeth Trump Grau: Her Life And Marriage To The Man Behind The SuccessUnderstanding The February 10 Zodiac Sign: Traits, Compatibility, And More
Florence Pugh Husband: Everything You Need To Know
Emma Stone Children: A Glimpse Into The Life Of The Oscar-Winning Actress
Eminem's Age: A Deep Dive Into The Life And Career Of The Legendary Rapper
Article Recommendations

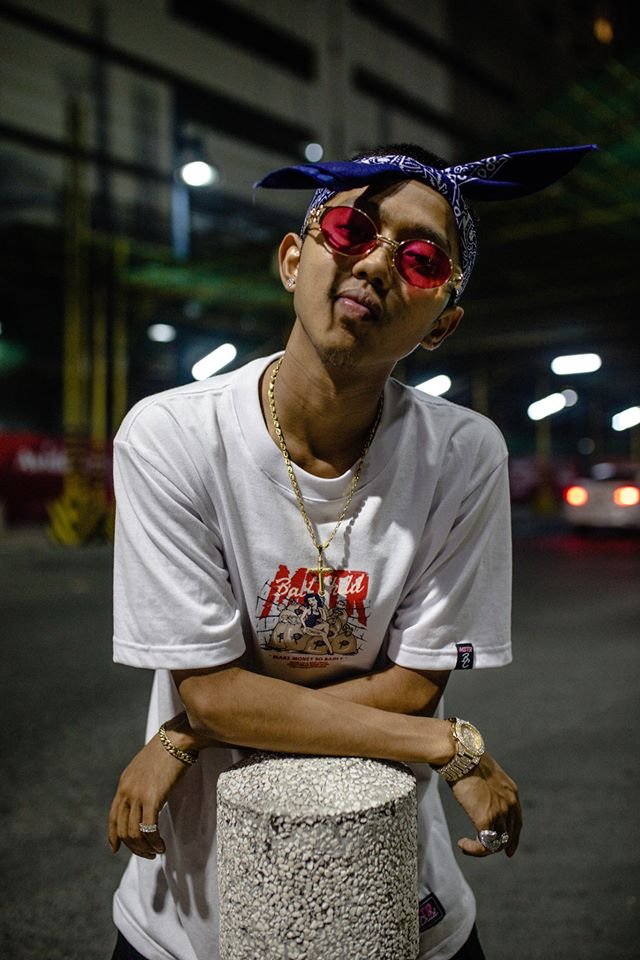
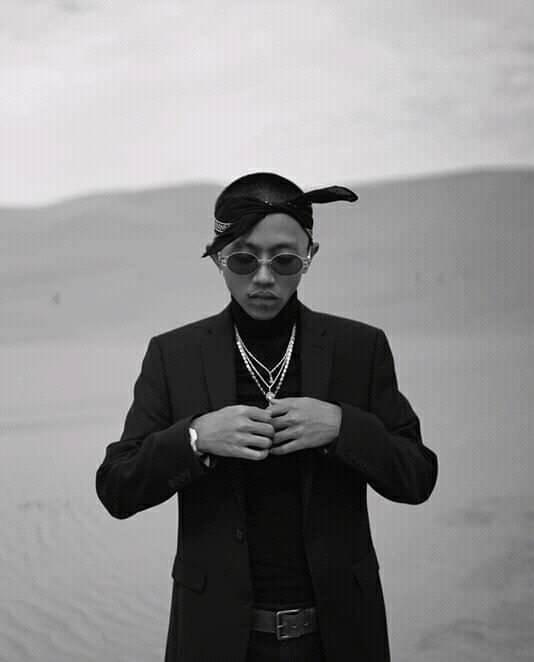
ncG1vNJzZmivp6x7rLHLpbCmp5%2Bnsm%2BvzqZmp52nqLumw9GenKVqZGSzrbvWZp5mmZeae6nAzKU%3D