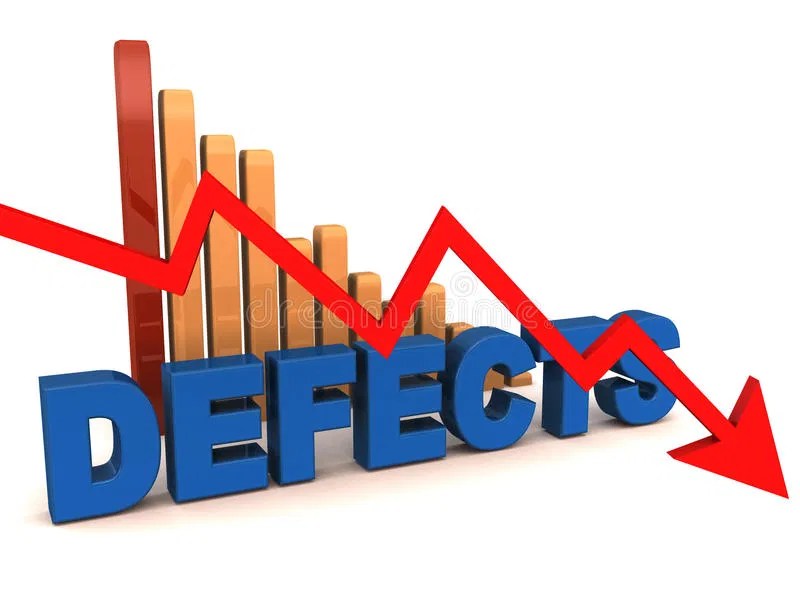
In today's competitive manufacturing landscape, achieving quality excellence is not just an aspiration but a necessity. Companies across various industries are striving to reduce defects and enhance their production processes. One remarkable achievement in this arena is the reduction of quality defects down to an astonishing 1 per 1 million pieces, representing a 350 percent improvement. This article delves into the strategies, implications, and methodologies that have led to this significant milestone in quality management.
This comprehensive analysis will explore the importance of quality control in manufacturing, the methodologies employed to achieve such remarkable results, and the long-term benefits for companies that prioritize quality. We will also examine the role of technology in facilitating these improvements, as well as the impact on customer satisfaction and brand loyalty.
As we navigate through the intricacies of quality management, we will provide actionable insights for businesses aiming to replicate this level of success. By understanding the principles that underpin this achievement, organizations can enhance their operational efficiency and reinforce their commitment to delivering superior products.
Table of Contents
Importance of Quality Control in Manufacturing
Quality control is a critical component of any manufacturing process. It ensures that products meet specified standards and customer expectations. Here are key reasons why quality control is vital:
- Minimizes Defects: Effective quality control reduces the likelihood of defects occurring during production.
- Enhances Reputation: Consistent quality builds trust with customers and enhances brand reputation.
- Increases Efficiency: By identifying and addressing issues early, companies can streamline processes and improve productivity.
- Regulatory Compliance: Many industries are subject to regulations that require stringent quality standards.
Methodologies for Quality Improvement
To achieve a defect rate of 1 per 1 million pieces, organizations often implement several key methodologies:
Six Sigma
Six Sigma is a data-driven approach aimed at reducing defects and improving processes. It uses statistical tools and techniques to identify and eliminate sources of variation.
Total Quality Management (TQM)
TQM is a holistic approach that focuses on continuous improvement in all aspects of an organization. It encourages employee involvement and emphasizes customer satisfaction.
Lean Manufacturing
Lean manufacturing aims to minimize waste while maximizing productivity. By streamlining processes and eliminating non-value-added activities, companies can enhance quality.
Technological Advancements in Quality Management
Technology plays a crucial role in achieving high-quality standards. Innovative tools and software have transformed the quality management landscape:
- Data Analytics: Advanced analytics enables companies to monitor processes in real-time and identify trends that may indicate quality issues.
- Automation: Automated inspection systems can detect defects quickly and accurately, reducing reliance on manual checks.
- Machine Learning: Machine learning algorithms can predict potential defects based on historical data, allowing proactive measures to be taken.
Benefits of Reducing Quality Defects
The benefits of achieving a defect rate of 1 per 1 million pieces extend beyond immediate cost savings:
- Cost Reduction: Fewer defects lead to lower rework and scrap costs.
- Improved Customer Satisfaction: Higher quality products result in increased customer loyalty and repeat business.
- Market Competitiveness: Companies known for quality can command premium prices and gain a competitive edge.
Case Studies of Successful Quality Initiatives
Several companies have successfully implemented quality improvement initiatives to achieve remarkable results:
Case Study: Toyota
Toyota's production system emphasizes quality at every stage. Through continuous improvement and employee training, the company has maintained low defect rates.
Case Study: Motorola
Motorola's Six Sigma initiative reduced defects significantly and set industry benchmarks for quality. The company's commitment to quality has enhanced its reputation globally.
Customer Satisfaction and Brand Loyalty
Quality is a key driver of customer satisfaction. When companies deliver high-quality products consistently, they cultivate trust and loyalty among their customers. Here’s how:
- Positive Reviews: Satisfied customers are more likely to leave positive reviews, enhancing brand reputation.
- Repeat Purchases: Customers who trust a brand are more inclined to make repeat purchases.
- Word-of-Mouth Marketing: Happy customers become brand advocates, promoting the brand to their networks.
Future Trends in Quality Management
The landscape of quality management is continuously evolving. Future trends include:
- Increased Use of AI: Artificial intelligence will play a larger role in predicting defects and optimizing processes.
- Sustainability Focus: Companies will increasingly integrate sustainability into their quality management practices.
- Greater Emphasis on Supply Chain Quality: As global supply chains become more complex, managing quality across vendors will be critical.
Conclusion
In conclusion, reducing quality defects down to 1 per 1 million pieces is a monumental achievement that can propel a company towards operational excellence and enhanced customer satisfaction. By implementing effective methodologies, leveraging technology, and fostering a culture of quality, organizations can not only achieve significant improvements but also secure their position in the market. We encourage readers to share their thoughts on quality management practices or explore other articles on our site to deepen their understanding of this essential topic.
Call to Action
We invite you to leave your comments below, share this article with your network, and check out our other resources on quality management and continuous improvement.
Thank you for reading, and we hope to see you back for more insights on enhancing your business practices!
ncG1vNJzZmivp6x7rLHLpbCmp5%2Bnsm%2BvzqZmm6efqMFuxc6uqWarlaR8ssHApaCtsV2Zsqexwq2qZpyfrLtuwM5maGaolad6cnnMoqOloZ%2BjerG1xJycrGWRYoB2fIypnKublaPBbrXMqamorpWisq%2FAjaGrpqQ%3D