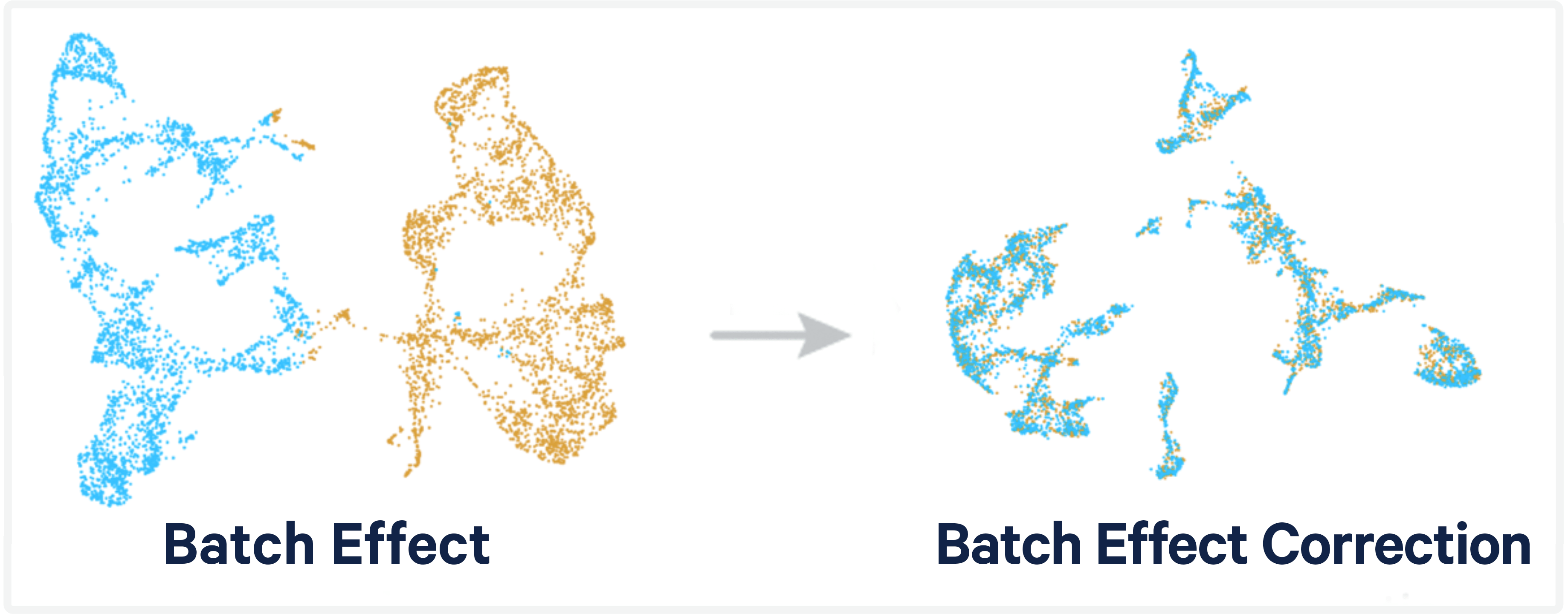
Understanding how a batch of raw material can impact the total annual carrying cost is crucial for businesses aiming to optimize their supply chain management. In today’s competitive market, companies must find ways to minimize costs while maintaining quality and efficiency. The carrying cost of inventory is a significant factor that directly affects a company’s profitability. This article explores the relationship between raw material batches and their influence on total annual carrying costs.
As we delve deeper, we will examine various factors that contribute to carrying costs, including storage, insurance, depreciation, and opportunity costs. By analyzing these elements, businesses can make informed decisions regarding their inventory management strategies. Furthermore, understanding these concepts can lead to more efficient production processes and ultimately, better financial performance.
In this comprehensive guide, we will discuss strategies to effectively manage raw material batches, the benefits of optimizing inventory levels, and how these practices can lower overall carrying costs. Let’s begin by defining what carrying costs are and how they relate to raw materials.
Table of Contents
Definition of Carrying Costs
Carrying costs, also known as holding costs, refer to the total cost of storing inventory over a period. These costs can include:
- Storage costs: Expenses related to warehousing and space utilization.
- Insurance costs: Premiums paid to insure the inventory.
- Depreciation: The decrease in value of goods over time.
- Opportunity costs: Potential income lost by tying up capital in inventory instead of investing elsewhere.
Understanding these costs is essential for any business that deals with inventory, especially those that rely heavily on raw materials.
Raw Materials and Inventory Management
Effective inventory management is crucial for businesses that depend on raw materials. The way raw materials are procured, stored, and managed can significantly impact carrying costs. Here are some key aspects to consider:
- **Just-in-Time (JIT) Inventory:** This approach minimizes inventory levels by purchasing raw materials only as needed.
- **Economic Order Quantity (EOQ):** A calculation that determines the optimal order quantity to minimize carrying costs.
- **Batch Processing:** Managing raw materials in batches can lead to economies of scale but may also increase carrying costs if not handled properly.
Impact of Batch Sizes on Carrying Costs
The size of raw material batches can have a significant impact on total carrying costs. Smaller batches may lead to higher frequency of orders, increasing transportation and ordering costs, while larger batches may result in higher storage and insurance costs. Here’s how batch sizes affect costs:
- **Smaller Batches:** Higher ordering costs but lower carrying costs.
- **Larger Batches:** Lower ordering costs but higher carrying costs.
Finding the right balance is key to minimizing overall expenses.
Components of Carrying Costs
As mentioned, carrying costs comprise several components. Let’s dive deeper into each of these:
Storage Costs
Storage costs include rent, utilities, and maintenance of warehouse facilities. Proper management of storage can significantly reduce these costs.
Insurance Costs
Insurance is essential to protect inventory against potential losses. Companies should regularly review their policies to ensure they are not overpaying.
Depreciation
Inventory can lose value over time, especially perishable goods. Businesses must account for this when calculating carrying costs.
Opportunity Costs
Investing in inventory means capital that cannot be used elsewhere. Understanding opportunity costs can help businesses make informed financial decisions.
Strategies for Optimizing Carrying Costs
To effectively lower total annual carrying costs, businesses can implement several strategies:
- **Inventory Audits:** Regularly assess inventory levels and turnover rates.
- **Supplier Relationships:** Foster good relationships with suppliers for better pricing and terms.
- **Demand Forecasting:** Utilize data analytics to predict demand and adjust inventory accordingly.
- **Automated Inventory Management Systems:** Implement technology to streamline inventory management processes.
Case Studies
Examining real-world examples can provide valuable insights into how businesses successfully manage raw material batches and lower carrying costs. One notable example is:
Case Study: Company A
Company A implemented a JIT inventory system that reduced their carrying costs by 15% within one year. By closely monitoring their raw material usage and streamlining their supply chain, they were able to minimize waste and improve cash flow.
Future Trends in Inventory Management
The landscape of inventory management is rapidly evolving. Key trends to watch include:
- **Increased Use of AI and Machine Learning:** These technologies can enhance demand forecasting and inventory optimization.
- **Sustainability Practices:** More companies are focusing on sustainable inventory management practices to reduce waste and environmental impact.
- **Blockchain Technology:** This can improve transparency and traceability in the supply chain.
Conclusion
In summary, a batch of raw material significantly affects total annual carrying costs. By understanding the components of carrying costs and implementing effective inventory management strategies, businesses can optimize their operations and improve profitability. We encourage readers to explore these concepts further, leave comments, and share their own experiences with inventory management.
As the business landscape continues to evolve, staying informed about these trends will be crucial for maintaining a competitive edge. Thank you for reading, and we look forward to your return!
ncG1vNJzZmivp6x7rLHLpbCmp5%2Bnsm%2BvzqZmm6efqMFuxc6uqWarlaR8onnBmqucoF2ks26%2BwLBkppmkmr%2BqrctmrqKknGKyp7LEnKtmpJ%2BssrN506irmqRdlruvwcClZJyZoqfGqrrGZpqoq6RjtbW5yw%3D%3D